Automatic Eyedrop Filling Machine Model: ALY Series
Eye Drops Filling Machine is a state-of-the-art technology designed for filling and capping 2-10ml eye drops. It incorporates several key technological features to ensure aseptic hygiene, it’s can CIP cleaning procedures, compliance with strict sanitary standards, and the use of robotic arms and vacuum technology for enhanced stability and precision.
- Airflow environment class A provided by the laminar flow hood
- Within the self-cleaning zone for the bottles, plugs, and caps
- Adopt aseptic gloves by operators for isolation operation
- Adopt six rotor peristaltic pump ensures accurate filling
- Automation control system enables the entire production process to operate automatically
- ALY-50
- ALY-100
Model |
ALY-50 |
Filling pump range |
2-10ml |
Filling nozzles |
2heads |
Plugging head |
one head |
Capping head |
one head |
Filling speed |
40-50bpm(depend on the filling volume) |
Filling accuracy |
±1% |
Supply voltage power |
380V/220V 50Hz 3.0kw |
Weight |
Around 1000kg |
Overall dimensions |
2600×1150×1700mm |
Model |
AFY-100 |
Filling pump range |
2-15ml |
Filling nozzles |
4heads |
Plugging head |
two head |
Capping head |
two head |
Filling speed |
80-100bpm(depend on the filling volume) |
Filling accuracy |
±1% |
Supply voltage power |
380V/220V 50Hz 3.0kw |
Weight |
Around 1000kg |
Overall dimensions |
2600×1150×1700mm |
Product Application
The application of the eye drops filling machine extend beyond eye drop manufacturing companies and are suitable for pharmaceutical plants and hospitals. It provides a reliable solution for eye drop production, ensuring product quality and safety, and delivering high-quality eye care products to consumers.
Aseptic system
The eyedrop filling machine is equipped with a laminar flow hood, which provides a controlled, sterile airflow environment. This helps prevent the entry of contaminants during the filling and packaging process. With the self-cleaning zone, the bottles, plugs, and caps are subjected to a purification process to ensure the cleanliness of the internal air. This process involves the removal of particulate matter, microorganisms, and other contaminants from the air to meet the required cleaning class standards.
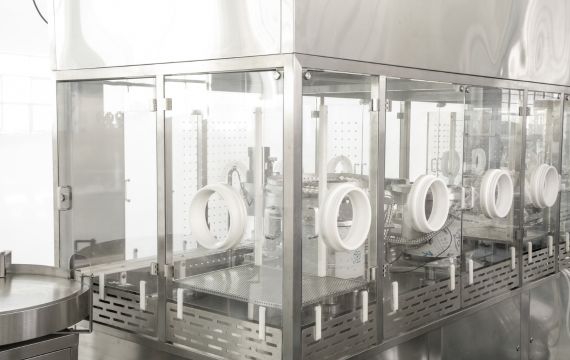
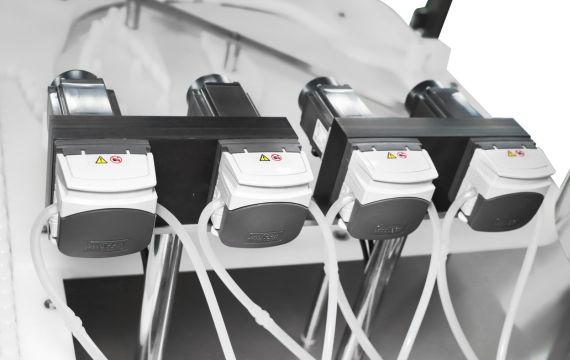
Filling system
The six rotor peristaltic pump provides precise and consistent control over the volume of liquid dispensed. Each rotor contributes to the pulsating action, ensuring accurate and repeatable filling measurements. The squeezing action of the pump on the flexible tube is gentle and minimizes any agitation or disruption of the liquid. This is particularly important for sensitive liquids or formulations that require careful handling to maintain their integrity.