Automatic Nose Drop Filling Machine Model: ALD Series
The cutting-edge nasal drop filling machine, the perfect solution for efficiently filling small doses of nasal drops. Designed with precision and productivity in mind, this rotary-type filling and capping machine is set to revolutionize your production process.
- Bottle rejection design
- No bottle, no filling, one bottle one filling
- Efficient and precise filling of small doses
- High sealing accuracy to prevent leaks
- Compliance with GMP standards for pharmaceutical
- ALD-50
- ALD-100
Model |
ALD-50 |
Filling pump range |
2-15ml |
Filling nozzles |
2heads |
Plugging head |
one head |
Capping head |
one head |
Filling speed |
40-50bpm(depend on the filling volume) |
Filling accuracy |
±1% |
Supply voltage power |
380V/220V 50Hz 3.0kw |
Weight |
Around 1000kg |
Overall dimensions |
2600×1150×1700mm |
Model |
ALD-100 |
Filling pump range |
2-15ml |
Filling nozzles |
4heads |
Plugging head |
two head |
Capping head |
two head |
Filling speed |
80-100bpm(depend on the filling volume) |
Filling accuracy |
±1% |
Supply voltage power |
380V/220V 50Hz 3.0kw |
Weight |
Around 1000kg |
Overall dimensions |
2600×1150×1700mm |
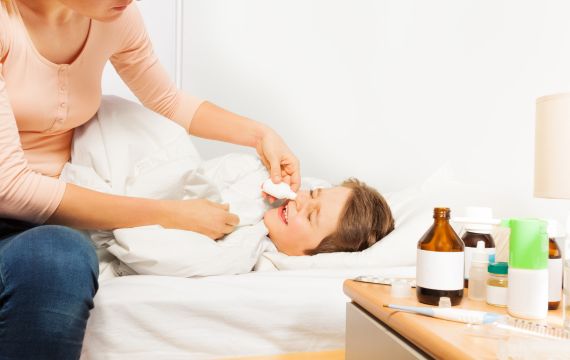
Product Application
In the pharmaceutical industry, nasal drops are a common form of medication used to treat nasal-related conditions. Our filling machine allows precise control of the dosage, ensuring the quality and consistency of each bottle. Whether you’re producing cold medicines, allergy medications, or nasal care products, our nose drop filling machine offers efficient and accurate filling services.
Robotic arm design
Using a robotic arm with vacuum suction technology swift and precise movements, combined with the vacuum suction technology, enable fast retrieval and insertion of the stopper and cap. This improves production efficiency and helps meet high-volume demands. The vacuum suction system provides a gentle and controlled grip on the stopper and cap, minimizing the risk of damage or deformation during the handling process. This helps maintain the integrity and quality of the components.
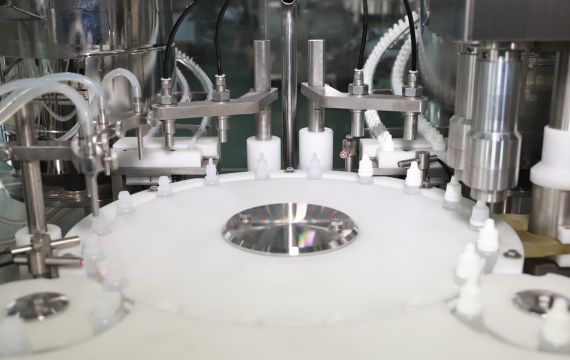
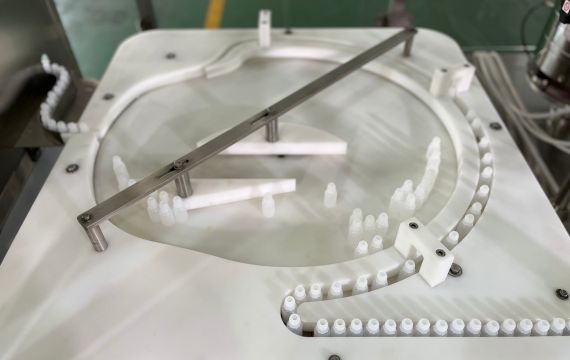
Bottle buffering area
The bottle buffering area minimizes the workload and pressure on operators. With the bottle buffering area in place, the filling machine can continue running for a period even when bottles are depleted. This eliminates downtime caused by a lack of bottles, increasing productivity and output. With bottle rejection design.